Basic Approach
At the Maruha Nichiro Group, we operate under a quality assurance system based on the Maruha Nichiro Group Philosophy and the Maruha Nichiro Quality Assurance Policy.
We prioritize the perspective of our customers, considering the “quality” they seek. Our goal is to deliver safe products and pursue food that ensures our customers' peace of mind.
Management Structure
The Maruha Nichiro Group has established a system in which the Managing Executive Officers' Committee is the highest decision-making body for quality assurance. It is also in charge of setting and implementing necessary quality assurance policies and initiatives. In addition, the Quality Assurance Committee has been established as an advising body to the Managing Executive Officers' Committee to deliberate on advisory matters.
The Quality Assurance Department at Maruha Nichiro, the central company of the Group, serves as the focal point of the Group's quality assurance by formulating various policies, monitoring and supporting improvements in management status through quality audits and product information maintenance, collecting and disclosing information on quality and labeling, and initiating employee training programs to increase quality awareness.
Responsible persons and persons in charge of quality assurance are appointed for each Company department and Group company to communicate information about Group policies and measures as well as to create and implement quality assurance plans and measures.
Quality Assurance Structure
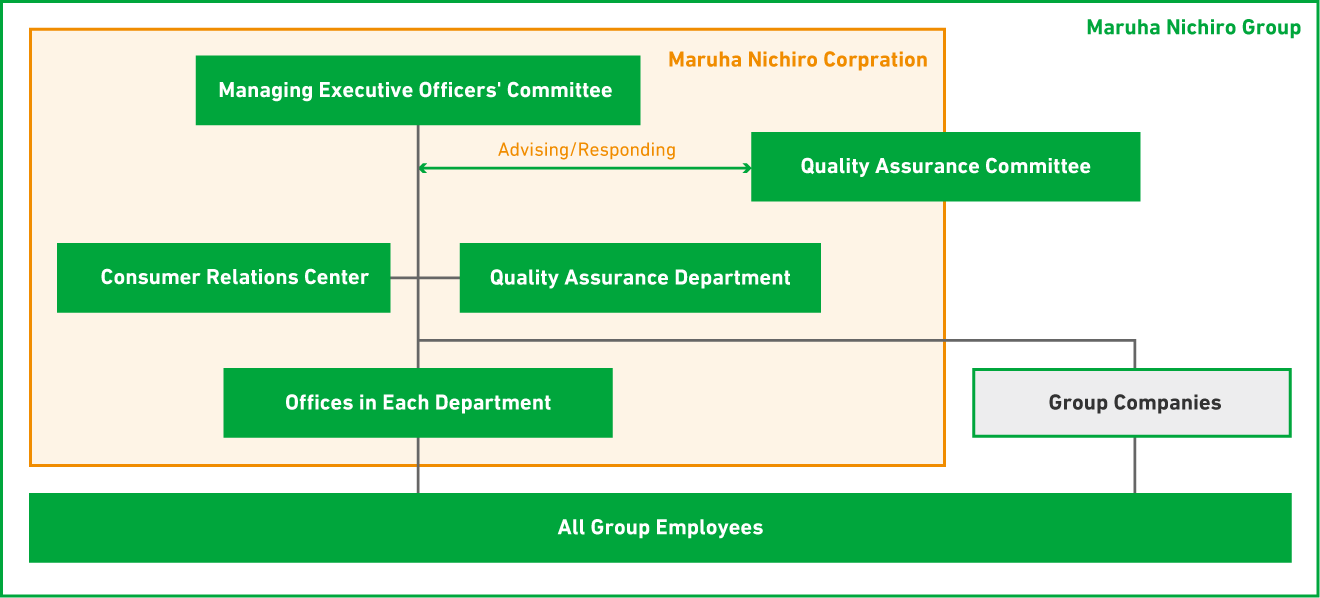
KGIs and KPIs from FY2022 to FY2030
Materiality: Provision of safe and secure food
Ideal state in 2030 (KGI): Providing safe food to people around the world

Achievement targets (KPI) | Target year | Target value | FY2023 | ||||||||||||||
---|---|---|---|---|---|---|---|---|---|---|---|---|---|---|---|---|---|
Achievements | Self-assessment | ||||||||||||||||
Serious quality-related incidents*1 (Domestic G*2) | 2024 | zero | Zero cases | ★★★★★ |
*1 Serious quality-related incidents are defined as product recalls announced in newspapers or on the Company's Web site due to violations of relevant regulations and voluntary codes as specified in GRI Standards 416-2 and 417-2
*2 Domestic G= Domestic Group Consolidate d Companies
Note: The department in charge is the Quality Assurance Department, Maruha Nichiro Corporation.
Message from Representative
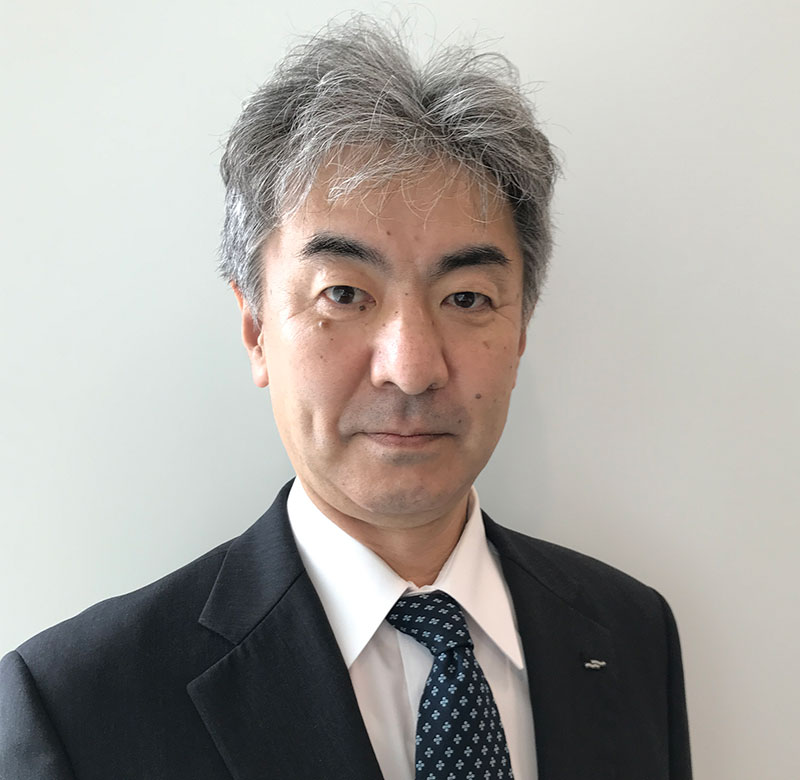
Tomoyuki Okumura
Quality Assurance Department
General Manager
The current fiscal year is the final year of the Medium-term Management Plan “For the ocean, for life MNV 2024.” In this Medium-term Management Plan, we have focused on reviewing and consolidating the foundation of our quality assurance systems by promoting activities aimed at achieving zero quality-related incidents, reviewing regulations, and launching the operation of our product information management system. As a result, we expect to achieve most of our KPIs. On the other hand, we recognize that further enhancement of our quality assurance systems is essential in the current so-called VUCA era in order to keep up with the fast-paced changes in the environment and continue providing safe and secure food at all times. We will expedite our efforts to address the issues that we are currently working on, including fostering a food safety and quality culture in which each and every Officer and employee involved in the value chain of Maruha Nichiro products considers food safety and quality as their top priority, and developing quality assurance systems for our overseas expansion.
Main Initiatives in FY2023
Product Incidents and Measures to Prevent Recurrence
The Maruha Nichiro Group achieved zero serious quality-related incidents*1 in FY2023. Our Group aims to provide safe and secure food while achieving zero significant quality incidents. To this end, we are strengthening plant audits and guidance for our manufacturing contractors, and we have obtained and maintained certification for our food safety management system at our production sites*2. In the external audits of our food safety management system conducted in FY2023, there were no major findings, and all minor issues were resolved within the specified deadlines. On the other hand, although we have not formally issued any product recalls, there were still complaints and problems that could have evolved into serious incidents if we had taken the wrong action, and reducing such incidents remains an issue for us. Since January 2022, we have been promoting efforts aimed at achieving zero quality related incidents with the aim of preventing serious quality related incidents so as to continue providing wholesome, safe, and healthy food. In FY2023, as part of our new initiative, we set up internal working groups from the viewpoints of “design and development assessment,” “purchasing management,” and “variable quality risk management,” and started issuing and implementing new regulations to strengthen the foundation of our quality assurance regulations. In addition, we formulated quality control standards (additional standards) based on an analysis of the causes of past complaints that could have led to serious quality-related incidents, and conducted reviews using the additional standards during regular audits of manufacturing partners from FY2024 in a progressive manner. We have established a system to prevent abnormal incidents and problems from upstream manufacturing processes and are shifting from the existing model of preventing recurrence of incidents to a preventive model of taking action before the occurrence of abnormal incidents.
*1 Serious quality-related incidents are defined as product recalls announced in newspapers or on the Company’s website due to violations of relevant regulations or voluntary codes as specified in GRI Standards 416-2 and 417-2
*2 Number of Maruha Nichiro Group bases certified under the GFSI standard: 31 bases (as of May 2024)
Standardizing Management Method for Product Specification Information
As Maruha Nichiro carries a wide range of product categories from foods that are close to raw materials, such as marine products, meat products, and agricultural products, to processed food that is consumed in a variety of settings, we have long faced the issue of having different methods for managing product specification information for different product categories. At the same time, the environment surrounding the food industry changes frequently, so there is a need to manage the latest product specification information and provide product information to customers promptly. In response to this, we have progressively introduced a new system that allows us to carry out the centralized management of everything from raw material information to product specification information and product information that we provide to customers. By utilizing this system, we will seek to provide accurate product information to customers and improve the efficiency of internal operations.
Promote Quality Education and Training
Overview of Quality Education and Training
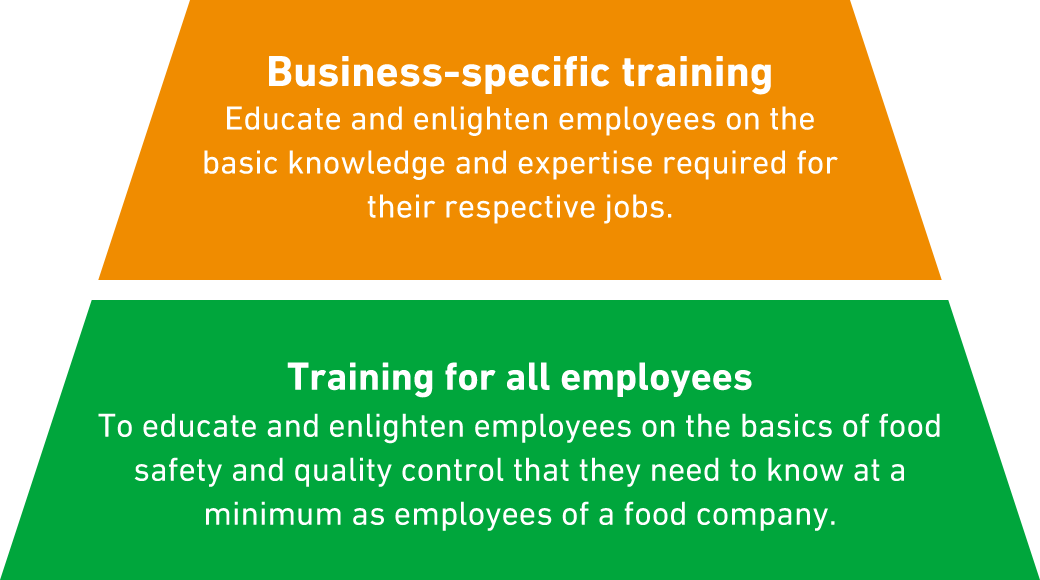
In order to improve the quality level of the value chain provided by the Maruha Nichiro Group, it is essential to enhance the awareness and knowledge of quality among all employees. A total of 10,351 employees participated in these training sessions.
In the future, we will further enrich the content and improve the quality of existing content to raise the level of education and training, as well as employee awareness and knowledge.

Type of training | Total sessions | Participants |
---|---|---|
Food label training (learning about universal guidelines, frozen food, shelf-stable food, seafood products, livestock products and practicing food label) | 14 times | 760 people |
Quality management workshops (factory hygiene management) | 5 times | 420 people |
Food defense workshops | 7 times | 635 people |
FSSC/ISO22000 standards study session | 1 time | 137 people |
FSSC 22000 internal auditor training (introductory training, skill advancement training) | 4 times | 97 people |
Food bacteria training | 2 times | 711 people |
Skills training for food bacteria inspectors | 1 time | 38 people |
Practical inspection skills training for food bacteria inspectors | 1 time | 4 people |
Customer service training | 5 times | 855 people |
Customer feedback monitoring training | 18 times | 6,586 people |
Customer service training | 2 times | 108 people |
Strengthening Factory Audits and Guidance
We ensure food safety and food defense by conducting audits, reviews, and guidance in the form of visits to manufacturing sites based on our proprietary standards that take into account the requirements of GFSI-recognized certification schemes (food safety management systems). In addition, we are expediting the provision of food not only within Japan but also globally. In order to respond promptly to qualityrelated issues arising from this, we have stationed quality assurance personnel in China and Thailand and are working on further strengthening our quality assurance systems in cooperation with local staff while maintaining close contact with each country/ region.
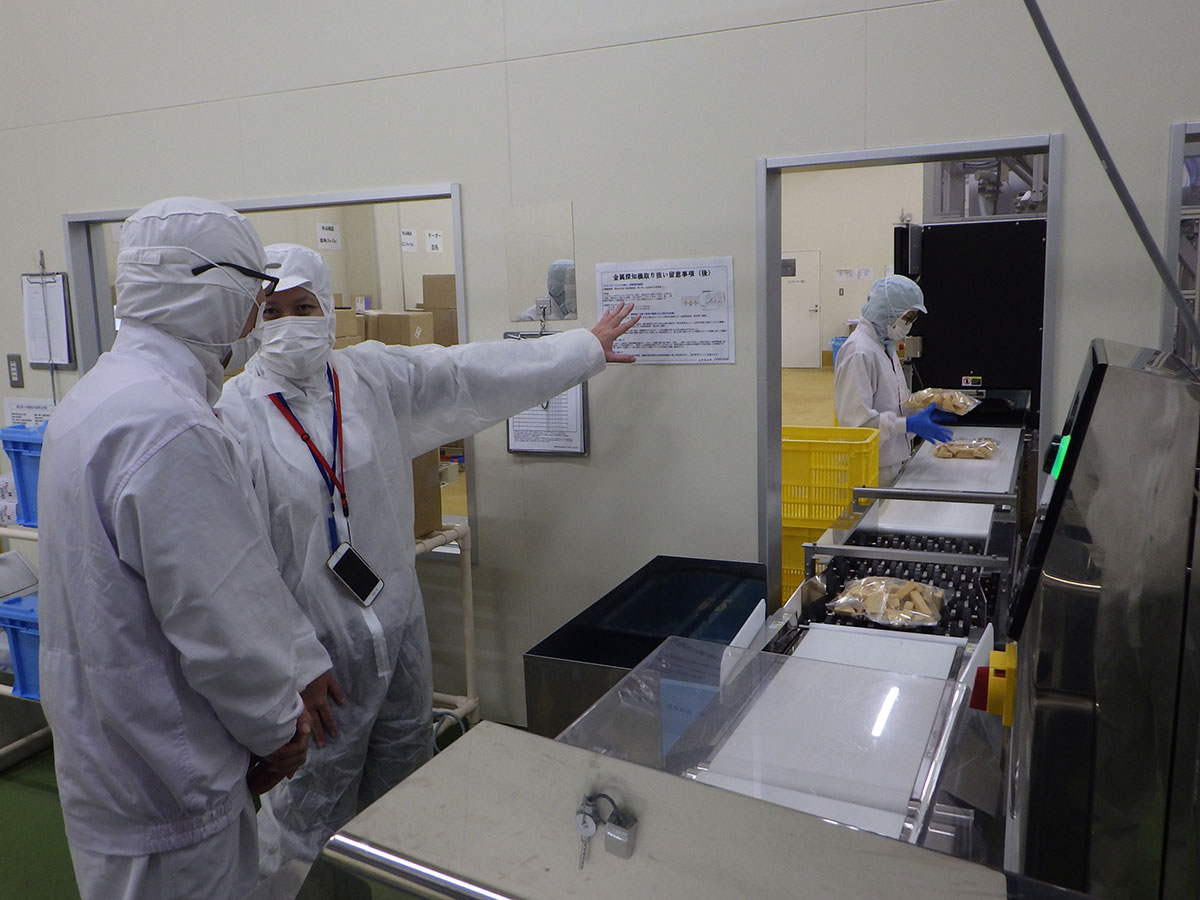
The inspection focuses on the production lines of certified factories and confirms sanitary management conditions through question-and-answer sessions with employees.